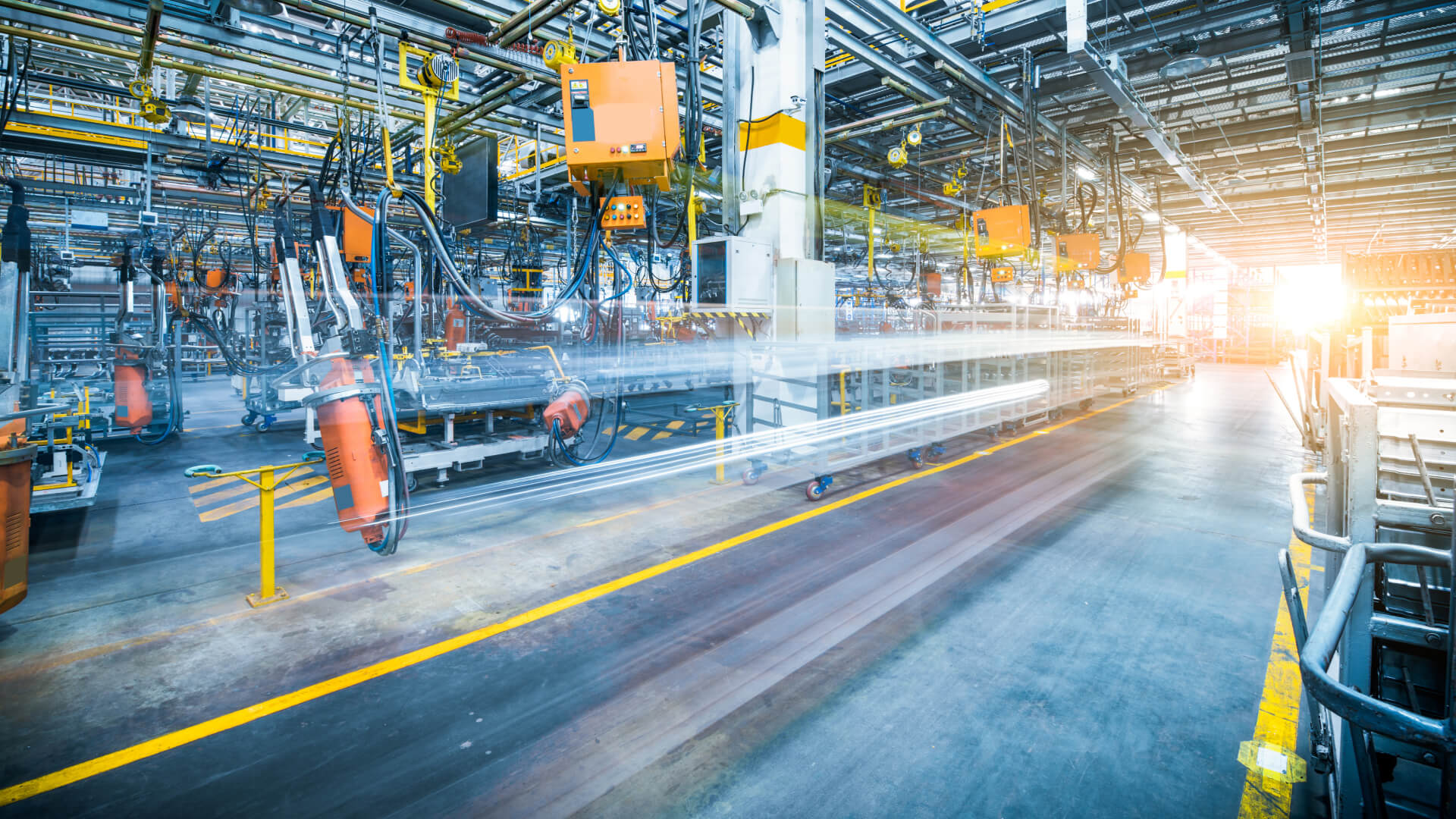
AIを活用した部品の予知保全!
ノーコードツールを活用してデータ分析の自走を目指す!
導入事例 No. 03
導入事例 No. 03
AIを活用した部品の予知保全!
ノーコードツールを活用してデータ分析の自走を目指す!
工場で部品の予知保全のためにAIによる劣化予測をに取り組んだ事例です。劣化の度合いを可視化し、部品の交換タイミングをサポートするAIの開発に取り組みました。また、Node-AIを使用することで、分析経験の浅い分析者の支援を行いました。
課題
- 経験のある技術者でなければ劣化しているか判断できない
- 劣化予測ができず最適なタイミングで部品の交換ができない
解決
- AIを用いて部品の劣化判断及び予測
- AIの劣化予測を用いて部品の交換時期を決定する
効果
- 経験のある技術者でなくても、部品劣化の判断及び予測をして発注等の作業を行える
- 最適なタイミングで部品交換をする事でコスト削減につながる
業種・業務
メーカー
工場
プラント
目的・手段
コスト削減
予知保全
予防保全
AIを活用して部品の予知保全をしたい
部品の交換にかかるコスト
工場では経年劣化した部品を不定期に交換する必要があります。部品を交換するためには工場を停止する必要があるため、計画的に行わないと生産計画に影響が出てしまいますが、部品の劣化判断は難しく予測できていないため対応が後手後手になっていました。
また、売上や生産量、出荷量といったデータを蓄積しており、DX推進の一環としてデータ活用に取り組んでいましたが、うまく活用することができないでいました。
また、売上や生産量、出荷量といったデータを蓄積しており、DX推進の一環としてデータ活用に取り組んでいましたが、うまく活用することができないでいました。
- 部品交換に関わるコスト
- 部品の劣化判断には経験のある技術者が必要
- 部品の劣化が予測できないため、計画的に部品交換を行えず、生産計画に影響が出る
部品の劣化をセンサー等で直接検知できない
しかしセンサー等で直接劣化を検知することはできず、経験のある技術者が原料の量、温度、生産量等から総合的に判断する必要があります。そのため
- 経験のある技術者でなければ部品が劣化しているか判断できない
- 部品の劣化を予測できず、最適なタイミングで交換できない
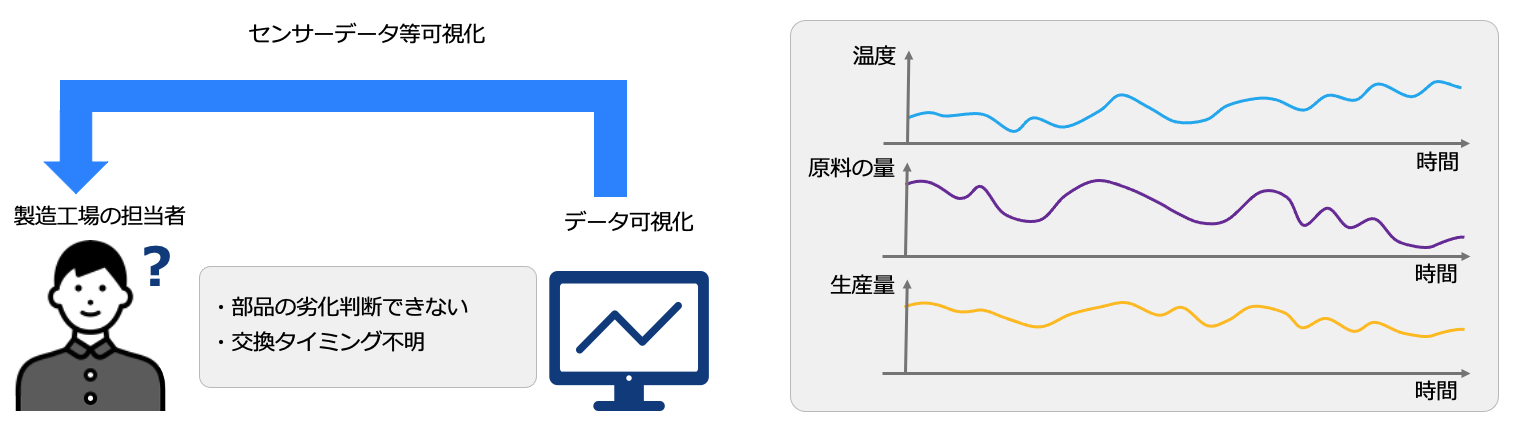
データを活用した部品の予知保全ソリューション
このような問題を解決する方法として「AIを用いた部品の予知保全」があります。機械学習を用いるとデータ間の関係性をAIモデルに学習させることが可能であり、今回の例では機器の稼働予定やセンサーデータから適切な部品の交換時期を予測できます。このソリューションによって
- 経験のある技術者でなくても部品の劣化を判断できる
- 交換に向けた準備を事前に行う事ができ、最適なタイミングで部品交換ができる
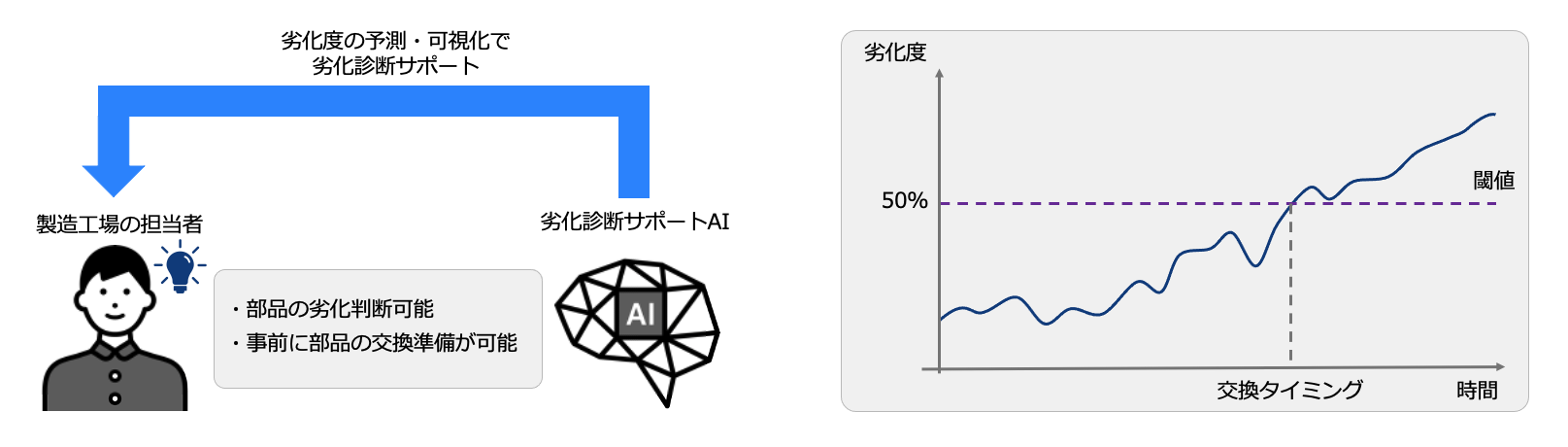
Node-AIによる効率的なAIモデル開発
経験の浅いデータ分析者を経験のあるデータ分析者がサポートする
データ分析には様々な落とし穴があり、気づかずに進めてしまって手戻りが発生する事がよくあります。
そのため、経験の浅いデータ分析者への経験のあるデータ分析者のサポートが重要となります。
Node-AIにはコラボレーション機能があるため、実際に処理を作成した人以外でも容易に処理の中身を確認でき、分析内容に関する深い議論がやりやすくなっています。
本案件ではNode-AIキャンバスを経験のあるデータ分析者が適宜確認し、議論しながら進めた事で手戻りなく進める事ができました。
そのため、経験の浅いデータ分析者への経験のあるデータ分析者のサポートが重要となります。
Node-AIにはコラボレーション機能があるため、実際に処理を作成した人以外でも容易に処理の中身を確認でき、分析内容に関する深い議論がやりやすくなっています。
本案件ではNode-AIキャンバスを経験のあるデータ分析者が適宜確認し、議論しながら進めた事で手戻りなく進める事ができました。
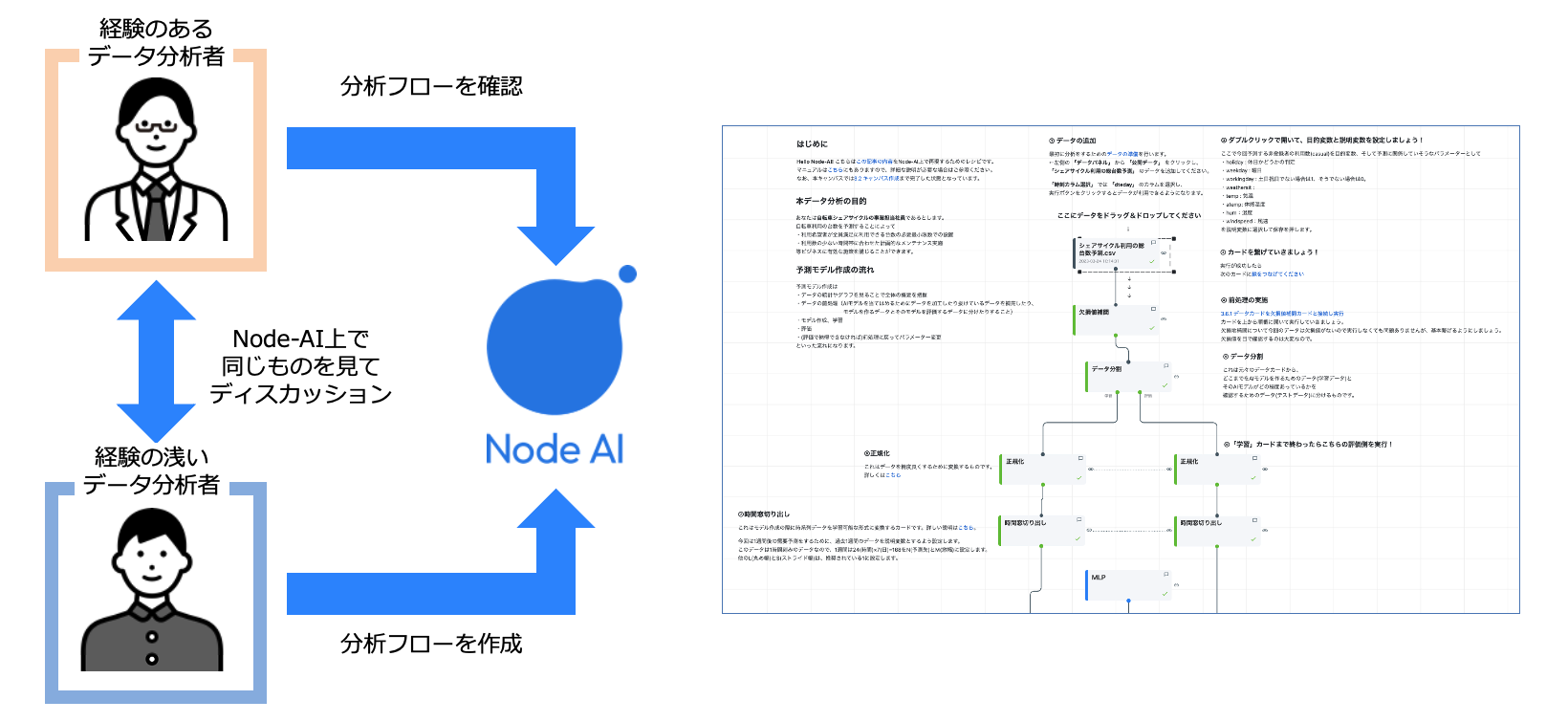
お客様が自走できるようなサポート体制
ドコモビジネスではNode-AIと合わせてデータ分析コンサルティングサービスも提供しています。
ドコモビジネスのデータ分析者がお客様側のデータ分析者とNode-AIを通して議論し、最終的にお客様側でデータ分析を自走いただくためのサポートサービスも提供しています。
ドコモビジネスのデータ分析者がお客様側のデータ分析者とNode-AIを通して議論し、最終的にお客様側でデータ分析を自走いただくためのサポートサービスも提供しています。
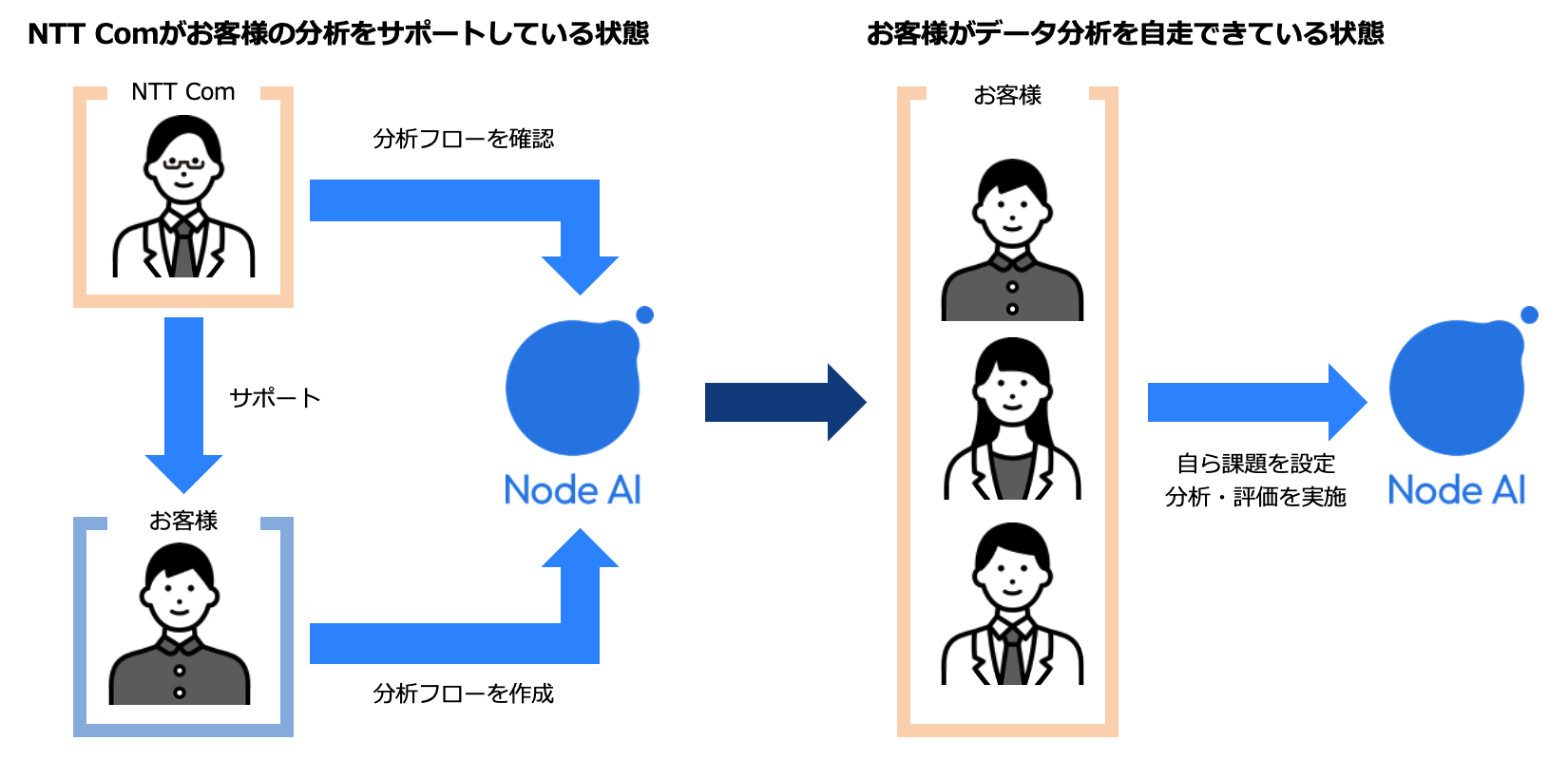
その他の活用方法
劣化や故障を判断するために必要なデータが揃っていれば、様々な状況でAIを活用できると考えています。
- プラント・工場
- 故障による突発的なプラント停止を防ぐための予知保全
- 機器のメンテナンスを効率化するための予知保全